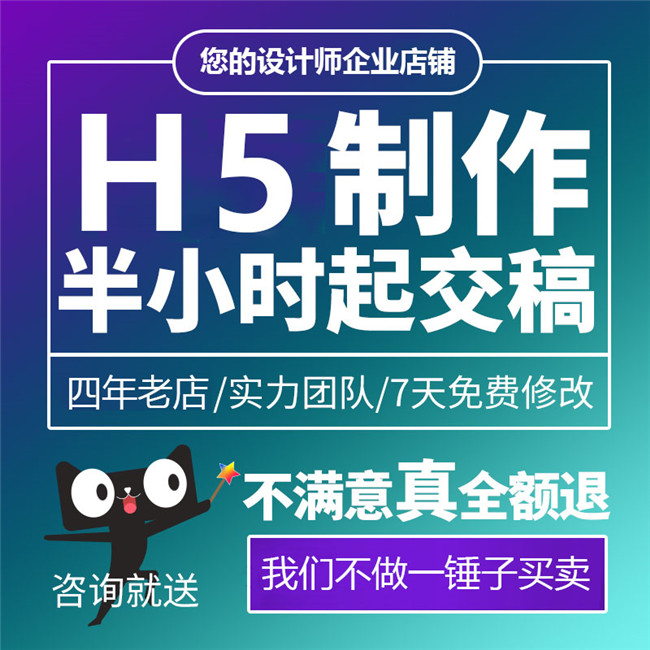
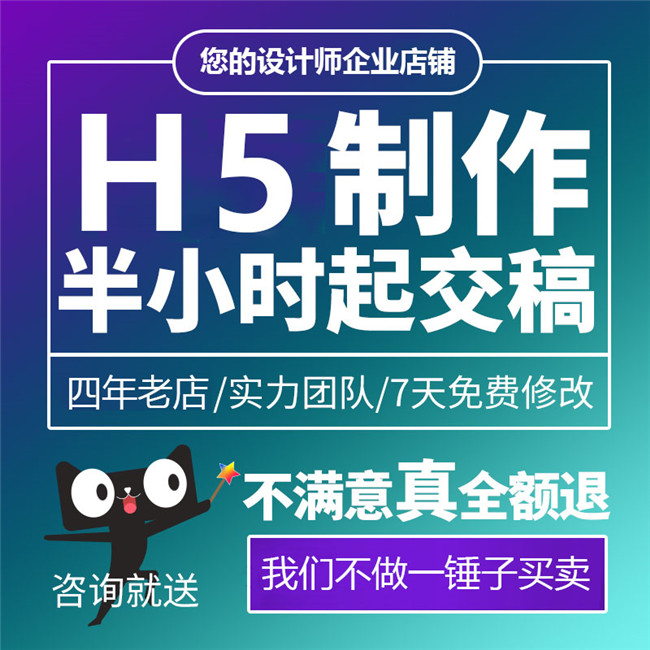
网友对于如何修复外圆磨床主轴,如何修复砂轮架主轴以及辽宁磨床静压主轴有用吗的相关性题,都有很高的关注度,下面小编为你整理了相关的题。
简介外圆磨床是金属磨削设备的一种,它具有生产效率高、性能好、加工精度好等诸多优点,因此受到很多用户的喜爱。然而,在使用外圆磨床时,不可避免地会出现一些题。主轴箱主轴间隙大、砂轮架电机平衡不良、砂轮架主轴磨损等。本文介绍外圆磨床主轴的相关内容。
外圆磨床加工工件时,通常将工件安装在两个中心之间并进行旋转。砂轮安装在砂轮架主轴上,以比工件更快的速度旋转。工作台可以以各种进给模式移动,使工件的整个长度在砂轮前面来回经过,直到加工出所需的工件直径。
它由床身、工作台、砂轮架、主轴箱、尾座组成,砂轮架是用来使砂轮高速旋转的关键部件,直接影响加工精度和表面粗糙度。一般是传动装置,由零件、主轴和轴承组成。下面我就以外圆磨床砂轮架主轴为例,简单介绍一下主轴磨损的原因及修复方法。
如何修理外圆磨床主轴
外圆磨床砂轮架主轴磨损的原因
外圆磨床的砂轮架主轴一般采用静压或动压轴承结构,液压油从吸油管进入轴承套油室,在轴承套与轴承套之间形成静压轴承。主轴轴承套左骨架油封用于主轴及静压轴承的液压密封。
外圆磨床砂轮架主轴加工工件时,如果进给速度过高,工作负荷过大,则在高速旋转时会对砂轮和工件施加冲击,使工件表面产生波纹或振动。工件表面、砂轮架主轴受到磨损,并磨出多条沟槽。这样,在砂轮架主轴正常旋转的情况下,液压油就会从砂轮架主轴的磨损部位漏出,造成外圆磨床漏油,造成现场混乱。
如果该外圆磨床使用频繁,砂轮架主轴漏油,加上之前保养不当,频繁更换静压轴承电枢油封,就会造成主轴与电枢接触。如果油封位置磨损更加严重,即使立即更换骨架油封,也无法有效防止主轴漏油题,甚至可能导致外圆磨床无法继续使用。
外圆磨床砂轮架主轴如何修理
由于外圆磨床的砂轮架主轴长期高速旋转,砂轮架主轴被磨出数条沟槽,有的深度可达3毫米。砂轮架主轴磨损部位出现泄漏,频繁更换架油封也无济于事,磨损更加严重,必须通过修复的方法解决。
如何修理外圆磨床主轴
修复方法一在骨架油封左侧、主轴左盖内侧加垫片,用垫片挡住或错开骨架油封磨损部位。由于主轴左端盖的装配位置受到,垫片的厚度不宜太厚,并应避免出现凹槽,因此必须设计专用垫片。和生产。由于空间有限,骨架油封的直径稍大,可将骨架油封稍微加工一下,装入轴承套左侧的浅槽中,这样既能保证密封,又能保证密封性。提高性能并进行大量维护。您可以避免管理任务并节省大量资金。
修复方法二拆开砂轮架主轴,用主轴磨出沟槽,然后磨削或拆喷。进行喷涂时,喷涂后需要进行二次加工,加工时对精度和同轴度公差的要求也比较严格,轮架主轴经过砂修后即可安装恢复使用。
外圆磨床主轴如何修复本文以砂轮架主轴为例,简单介绍外圆磨床砂轮架主轴磨损的修复方法。本文介绍两种恢复方法。第一种方法有效且恢复过程快,但有一些局限性。方法2较为保守、可靠,但成本较高,维修周期较长。在修复过程中,可以根据实际情况采取合理的修复方法。了解更多外圆磨床主轴,请关注捷众机器人。
曲轴加工技术的发展历史是怎样的?20世纪70年代之前,粗加工发动机曲轴所采用的加工方法是在多刀车床上车削曲轴主轴颈和连杆轴颈。这种方法加工精度低、灵活性低、加工质量稳定性差、内应力大,难以达到合理的加工余量。粗加工后通常需要消除应力和回火以消除应力。因此,在粗加工时,必须为后续的精加工工序留有较大的加工余量,以消除弯曲变形。曲轴精加工一般采用常见的磨削工艺使用MQ8260曲轴磨床粗磨-半精磨-精磨-抛光。手工操作通常会导致加工质量不稳定、不良率较高。
20世纪70年代到80年代,随着数控车削和数控外圆铣削用于曲轴粗加工,加工条件得到改善。精加工仍以常规磨床研磨技术为主。
20世纪80年代中期,数控内铣工艺重新出现,数控内铣的品质因数高于数控外铣,特别是对于锻钢曲轴,内铣更有利于断屑。精加工工序多采用半自动曲轴磨床,头座、尾座同步驱动,一定程度上提高了加工精度。
1985年至1990年,开发了曲轴车削和车削车削工艺,具有精度高、效率高的优点,特别适用于不需要侧面加工、有退刀槽的平衡配重。对于带有轴颈槽(包括轴向底切)的曲轴,机加工后可以立即对曲轴进行精磨,从而无需进行粗磨工序。曲轴精加工采用少量数控磨床磨削技术,提高尺寸一致性。
20世纪90年代中期,发展了数控高速外铣,对于平衡配重方面需要加工的曲轴,比数控车削、数控内铣和车床车拉具有更高的生产效率。另外,数控车-车工艺需要两道工序加工连杆轴颈,而数控高速外铣可在一道工序中完成,具有切削速度高达350m/min、切削时间短等优点。时间等等。有这个。并缩短加工循环时间、减小切削力、降低工件温升、延长刀具寿命、减少换刀、提高加工精度、增加灵活性。因此,数控高速外铣将成为曲轴主轴颈、连杆轴颈粗加工的发展方向。精加工采用数控磨床,采用静压主轴、静压导轨、静压丝杠砂轮头座、直线格子闭环控制等控制装置,保证尺寸公差和形位公差稳定,超精加工还包括数控采用砂带抛光机,超精加工后的曲轴轴颈表面粗糙度提高一级以上精度。
CBN高速磨削是在20世纪90年代开发的。英国LANDIS生产的曲轴磨床,磨削速度高达120m/s,采用剥皮方式,一次装夹只需几分钟即可完成从粗磨到精磨。这将导致磨削代替其他粗加工工艺的新局面。
21世纪初,复合加工技术进入曲轴制造行业。复杂机床必须具备工序集成能力和多加工集成能力。奥地利WFL公司生产的卧式车铣复合加工中心(图3)展示的是M40G型号。在曲轴硬化之前,“一次夹紧,全部加工”。加工好的曲轴可以直接交付到精加工工序。即使在曲轴精加工方面,CBN数控磨床也有一体化工艺。这意味着所有曲轴主轴颈和连杆轴颈均通过一次装夹中的摆动跟踪进行磨削。
纵观上述演变,我们可以看出曲轴加工技术正在向高速、高效、复杂化方向发展。目前应用最广泛的粗加工工艺是主轴颈采用车-车工艺加高速外铣,连杆颈采用高速后续外铣。全部采用干式切削和精加工。采用数控磨床加工而成,具有自动送料、砂轮自动修正、自动尺寸和圆度补偿、自动分度、两端电子同步驱动等功能。可一次夹紧磨削主轴颈和连杆颈,并采用带尺寸调节器的数控砂带磨床进行超精加工。
常见曲轴加工先进设备数控高速随动外圆铣床性能介绍介绍型号为VDF315OM-4的高速随动外圆铣床的性能。该机床是德国勃林格公司专门针对汽车发动机曲轴设计制造的柔性数控铣床,采用工件旋转与铣刀进给伺服联动控制技术,可在不改变曲轴旋转中心的情况下实现一次装夹。使您能够跟踪和追踪铣削曲轴上的连接。杆轴颈。采用一体式复合结构床身,由电磁驱动工件两端同步旋转,具有干式切削、加工精度高、切削效率高的特点。采用SIEMENS840DCNC控制系统,设备操作说明如下通过输入零件的基本信息,显示在人机界面上,参数自动生成加工程序,可加工长度450-700毫米、回转直径380毫米以内的各种曲轴。杆轴颈为002mm。
数控车削-车削机床该设备可一次完成全部同心车削,车削-车削侧面加工可在同一台机床上完成,加工效率高。采用特殊的卡盘和刀具系统,还实现了柔性加工,使机床维护简单,维护成本低,特别适合不需要配重侧加工且轴颈有退刀槽的曲轴。其中,拉削工艺可以用高效的梳齿车削工艺代替(图5),梳齿加工一般放在工艺的最后阶段,通过微量径向进给和纵向车削实现高速精加工。
曲轴推力面滚压机该设备用于旋转滚压曲轴推力面,具有以下技术特点推力面滚压抛光并在线测量,以滚压和抛光代替磨削,可同时进行。对于时间车削加工,在刀头上安装滚动抛光装置以提高精度。目前性能较好的设备有德国HEGENSCHEID公司的专用曲轴止推面滚压机。
数控曲轴磨床以德国欧文容克机械制造有限公司的JUNKER摆动跟踪系列磨床为例,该设备采用CBN砂轮与油冷曲轴的组合进行高速加工。适用于汽车发动机曲轴加工,质量稳定。主要功能是加工过程中轴颈圆度和尺寸的检测和修正,具有“学习功能”的控制系统,附加圆度偏差和干涉量的自动补偿。可补偿的过盈量是由于温度、机械和功率的影响、磨削公差的变化、材料和金属结构的变化、砂轮的可加工性和机床的磨损状态、主轴颈磨削和连接而产生的。连杆轴颈同时固定,理论偏差0;切入磨削和摆动磨削;为了支撑“敏感工件”,主轴上使用了自定心三点稳定支架。CNC控制的冷却液供应确保磨削区域的长期使用。恒压圈采用式导轨,无爬行现象,持久高精度磨削主轴适合以高达140m/s的速度进行磨削。
在上面介绍的先进设备中,我们可以看到一个共同点高速、高效、柔性,适合当今多品种、小批量产品的发展趋势。由于曲轴加工与一般加工不同,所以上面介绍的内铣、车削、高速外铣等很多工序都必须使用专用刀具。制造和价格也很高并且相对昂贵。如果产品改造包括改变曲轴结构,则必须使用新刀体加工曲轴,影响产品开发周期和制造成本,最终导致产品缺乏竞争力。现在瓦尔特和其他刀具制造商已经开发出一种灵活的专用刀具,用于曲轴制造的模块化刀具。产品开发周期显着缩短,制造成本降低。
敏捷柔性曲轴生产线AFTL解决方案探讨目前,国内汽车曲轴生产线大多为FTLFlexibleTransferLine,即高速柔性生产线,该生产线的特点是不仅可以加工同系列的曲轴,而且还可以加工同系列的曲轴。也非常灵活,因为它可以处理变体、替代品和新产品。为了进一步提高高速柔性生产线的生产效率,更快地适应市场,FTL的下一步开发是敏捷柔性生产线AFTLAgileFlexTransferLine。主要目的是
满足不断变化的市场需求。不仅满足当前产品的需求,还考虑到未来市场的需求。
符合生产方法的要求。能够满足现代发动机生产“多品种、大中批量、高效率、低成本”的需求。
它符合“精益生产”的原则。停止浪费,以最小的投入、最大的回报追求利润。
笔者认为,由于发动机曲轴本身的特殊结构,曲轴AFTL应具有以下特点。它由高效专用机床组成,包括高速加工中心和少量复杂机床。机床按照工艺流程布置,通过自动输送装置连接,采用灵活的夹具和高效的专用工具进行生产。为防止主工序因设备故障而导致整条生产线停工,可增设并联设备,以满足批量生产的需要。接下来是工艺流程的金属加工部分。
铣端面、确定总长度、钻质心孔、车大、小端外圆铣主轴颈、轴肩铣连杆颈、轴肩车削主轴颈、沉槽车削连杆颈、轴肩锪孔枪油孔钻孔清洗滚圆角法兰钻孔攻丝主轴颈CBN精磨连杆颈CBN精磨小端斜切磨削法兰端斜切磨削车削滚压推力表面、铣键槽动平衡主轴、连杆、法兰外径砂带抛光清洗、冷却检测分级。
与上述工艺流程相关的一些题讨论如下曲轴质心孔和几何中心孔的选择。
毛坯质量好,加工公差小,加工公差分布均匀。此时曲轴的质心孔与几何中心孔基本重合,因此无需花费大量资金购买质心设备并自己钻几何中心孔。亮;由于毛坯质量差,加工余量大,且加工余量分布不均匀,应优先考虑质量中心孔。由于初始不平衡量较大,钻几何中心孔会导致质量分布不均匀,转动惯量较大,影响后续加工设备的精度。另外,如果采用几何中心孔进行动平衡,则初始不平衡量可能超过平衡机的要求而无法平衡。在这种情况下,首选质量定心机。
合理选用曲轴粗加工机床选用原则先进金属加工设备在曲轴制造中的重要性是毋庸置疑的。能可靠保证尺寸精度和一致性,适应生产节奏要求,提高整体工艺水平。但我们不能采取“一刀切”的做法,这并不是说设备越先进越好,我们必须坚持以下三个原则1、本着工艺原则,结合产品结构,能满足尺寸精度和一致性的要求。2按照经济效益原则,采用招标方式降低成本。3、遵守设备管理和维护原则,定期检查设备制造商的A/S质量和设备安装部件的供应情况。
合理组合国内曲轴生产企业对设备引进存在一些误区,比如认为设备越先进、越贵越好。事实上,高科技设备如果使用不当,不仅无法发挥其作用,还会造成浪费。下面以数控高速外铣、数控内铣、数控车削的合理组合为例。
曲轴平衡块侧面必须加工,加工主轴颈应先采用数控内铣或数控高速外铣,加工连杆颈应采用数控高速外铣。如果毛坯是锻钢毛坯,采用数控内铣更有利于断屑。不宜采用数控车削,崩刀现象严重,因为配重侧间歇旋转,且曲轴转速很高,约为1000转/米。
曲轴平衡重侧面不需要加工,采用数控车床进行主轴颈加工比较合理,加工精度高。与六转曲轴一样,连杆轴颈轴线不在同一中心线上,这给车床车削加工带来了题,因此数控高速外圆铣削更为合理。
对于轴颈有退刀槽的曲轴,数控车削占主导地位,而轴向有退刀槽的曲轴不能用数控高速外铣和数控内铣加工,但可以用车削加工。
上述设备需要采用独立双刀盘、模块化刀具系统等实现柔性加工。
曲轴圆角滚压强化曲轴圆角滚压强化主要是为了改善曲轴疲劳。
发表评论