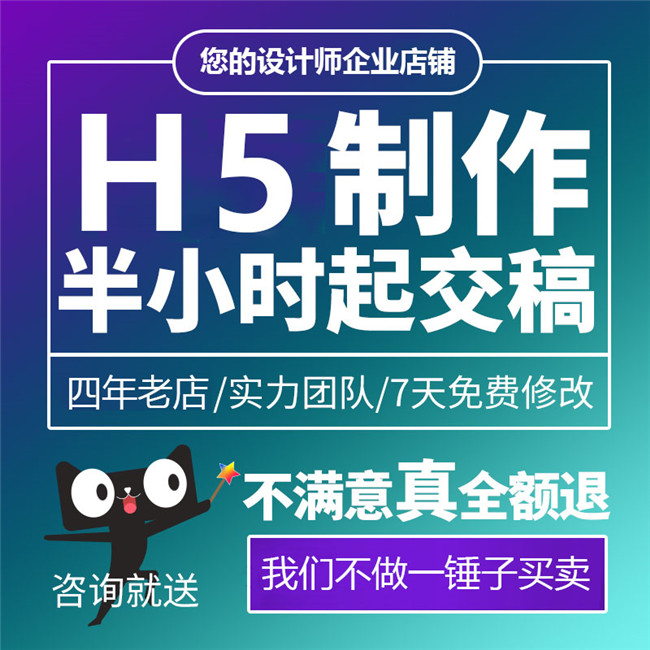
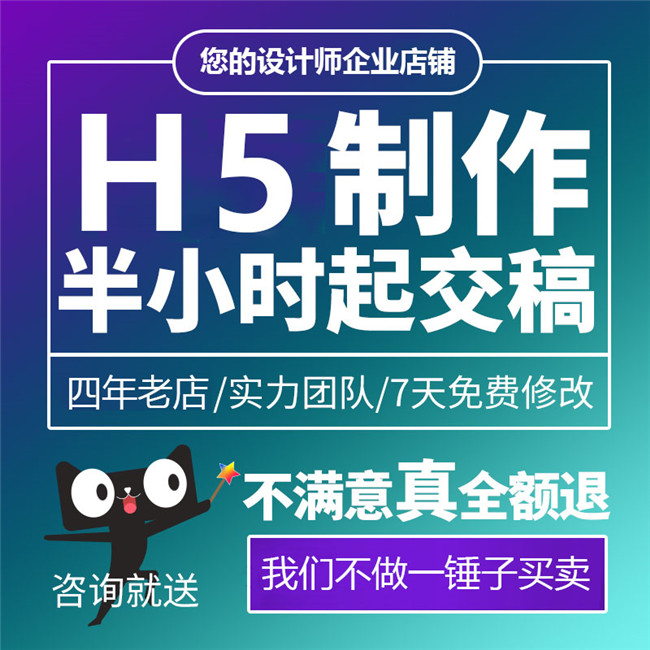
不少人都想知道制造过程中的质量控制的题,关于生产工具控制记录这类题,小编为你介绍一下吧!
介绍
生产质量控制是指管理制造过程中执行的所有活动以达到质量要求。
生产质量控制是生产运营管理的重要方面之一,无论你生产多少产品,交货时间多么及时,如果生产出来的产品质量不达标,那就没有多大意义了。
1、各级生产人员的质量责任
1、生产部对质量负责。
1、全面监督产品制造过程的质量控制工作。
2、处理好各车间的质量控制和质量题,在生产过程中衔接起来,努力改善生产质量状况。
3、组织对各车间质量控制绩效的考核和车间管理人员对质量控制任务的工作评价。
4积极配合品管部门的工作,协调各车间的质量工作。
5、制定生产系统质量管理体系并监督实施6、组织技术培训,提高生产线操作人员的操作能力,减少质量事故的发生。
7、按照公司规定对本部门质量事故进行分析和处罚。
2、车间管理人员的质量责任
1、负责所辖工作场所的质量控制工作。
2监督检查班组长执行质量管理规定的情况。
3、对班组内部出现的质量题进行原因调查,追查责任人。
4、负责报告工作场所的质量事件或质量控制绩效。
5、向有关部门报告生产过程中出现的物料质量题。
6、在工艺设计过程中,分析影响产品质量的题并提出意见。
7、防止可能发生的质量事故。
8、指导车间工作,将质量合格率控制在规定范围内。
3、基层管理者的质量责任
1、全力配合生产主管,确保质量控制。
2、检查和监督操作人员是否严格按照《操作规程》进行工作。
3、对辖区内的生产线,特别是质量题多发的工序和操作点进行检查。
4、及时将检测结果告知被检测员工,督促改进。
5.识别质量趋势。
6、及时控制质量题的不良趋势。
7、就地管理质量维护,明确各责任人的职责。
8专业品质控制人员帮助掌控全局。
4、生产线操作人员的质量责任
1、严格按照《作业指导书》进行作业,杜绝不合格品的发生。
2、制造过程中如发现不合适材料,及时向班组长报告。
3、在作业过程中,我们按照质量标准对本部门工作流程中的产品进行自检。
4.运行过程中,会进行相邻进程的交叉检查。
5、发现有质量题的产品必须及时返工、纠正错误。
2、生产制造过程的质量控制
制造过程是直接形成产品质量的过程,建立能稳定生产高质量产品的管理网络,在各个环节进行质量保证和预防,监控因素是过程管理的关键。控制影响产品质量的一切。
1、合理调整生产时间
在组织生产工作时,必须合理分配生产时间,长时间连续加班容易使工人疲劳,增加生产中出现差错的可能性。
2、加强过程管理
严格的工艺纪律,全面控制生产制造过程的质量保证功能,确保生产制造过程始终处于稳定受控状态,并不断进行技术创新和工艺改进。
为了保证加工工艺质量,生产管理人员必须勤勉地进行文明生产、平衡生产,合理配置工作站设备,保证加工过程中有良好的工作环境。
三、技术检验工作的组织
为确保产品质量,必须按照技术标准对原材料、在制品、半成品、成品和工序进行质量检验,严格控制,杜绝不合格原材料投入生产。不合格的产品不予调拨,合格的半成品不予使用,不合格的零部件不予组装,不合格的成品不予出厂,其产值和产量不计算。
四、加强技术指导和教育
为了加工生产出高质量的产品,生产人员特别是工人必须具备一定的技能和熟练的工作能力,而这些能力的形成有赖于工作经验和企业培训。
五、加强岗位管理
生产部门各级管理人员要以经营管理为主,健全监督检查制度,加强生产现场检查,发现题立即制止,并追究责任人员责任。
6.了解质量趋势
为了充分发挥质量管理在生产制造过程中的预防作用,需要系统地识别一定时期内企业、工作场所、团队的质量状况和发展趋势。
识别质量动态的有效方法是对质量状况进行全面的统计和分析,这就需要建立和完善质量源记录。
合格产品到仓库的转移和交付以及不合格产品的修理和处置必须有记录并形成文件并由质检代表出具证明。
质量部门应定期进行汇总统计,并根据原始记录分析质量变化的原因,以便公司各级管理人员和员工及时识别质量趋势。
7加强不合格品管理
加强不合格品管理,要重点做好以下工作
1、妥善处理不合格品的各种情况,并保存原始记录。
2定期召开不合格品分析会议。通过分析研究,找出不合格品产生的原因,吸取教训,制定措施,防止再次发生。
3、根据原始质量记录,对不合格产品中的报废品、返修品、回收品等进行分类统计,并对报废品的种类、数量、消耗的劳动力和原材料、负责人进行分类。对废品产生情况进行统计,将各种数据汇总整理成表格,为后续的单项、综合分析提供依据。
4.建立不合格品(包括报废品)的技术档案。
实施过程质量控制。
3、二次生产过程质量控制
企业辅助生产流程主要包括材料供应、工具供应、设备维护等。这些操作的质量直接影响制造过程的质量。企业要注重提高这些辅助环节的工作质量。
具体行动包括
1、材料供应质量控制
加强仓库管理
物料到达工厂、仓库必须按照质量标准进行检验和批准,并加强仓库管理,防止物料错放、混用和质量变质,防止使用过程中发生质量事故。
严格检查
属于外购或委外材料的,必须经过仓库检验或寄售检验,不合适的材料必须退回或认领。
供应调查
对于大批量关键物料,请在确认订单或购买前,亲临货源地考察了解物料质量及设备的质量保证体系。
建立质量控制联络点
定点供应、定点外包对于制造商来说,可以建立定期、固定的质量控制联络点。
2、刀具供应质量控制
工装包括刀具、模具、夹具、量具、切削刀具等各种外购标准刀具和自制非标刀具。
定期检查
为保证标识准确,应在当地计量部门统一组织下定期进行检查。为了巩固企业的计量值,企业必须有专门的部门负责计量器具的购置、保管、发放、鉴定、校准和修理。
制造过程中严格的质量控制
生产所需的众多非标工具和各种工艺设备通常是在制造部门制造的。制造过程的质量控制必须按照产品制造过程的质量控制要求进行。
自制非标工具仓库管理
自制非标工具竣工验收合格后,送入仓库存放备用。已经存在很长时间的工具通常面临着如何在使用过程中保证其质量的题。对于这些工具,仓库一般需要采取借用的方式,并进行统一管理。仓库应设置工具卡,记录使用部门、使用负责人、使用和消耗日期、借出和归还情况。用户使用后必须将工具退回仓库,仓库必须确认工具已检验合格,经检验发现有损坏或不符合质量要求的,必须修理或报废。
长期使用的工具应定期到使用场所检查,发现质量题及时处理。
密集锐化
大量消耗的刀具必须进行精磨,以保证刀具的质量。对于耐用、昂贵、复杂的切削刀具,更应注意采用上述刀具管理方法,以保证质量。
3、设备维修质量控制
设备使用及维护
生产人员要正确使用设备,精心维护,及时消除风险隐患,保持设备完好率在90%以上。
建立设备维护团队
要有专门的设备维护队伍负责生产。
确保设备符合指定的质量标准
正如公司的设备维修部门在维修设备和工具时要确保产品质量一样,也必须确保维修后的设备符合规定的质量标准。
设备维护人员与日常生产活动密切相关,对保证设备质量和产品质量发挥着重要作用。
在质量控制要求方面,设备维护人员必须
首先,要经常对设备进行检查,快速发现和解决设备隐患,防止设备故障。
二是配合生产人员正确使用和维护设备,生产人员主要进行初级维护,维修人员主要进行二次维护。
三是抢修损坏设备,对关键设备进行抢修。抢修必须及时、快速,抢修设备质量必须符合标准。
在
制造过程中的质量控制和一些关于生产工具控制记录的相关题,今天就讲解这里了,如本文对大家有所帮助,记得关注订阅本站。
发表评论