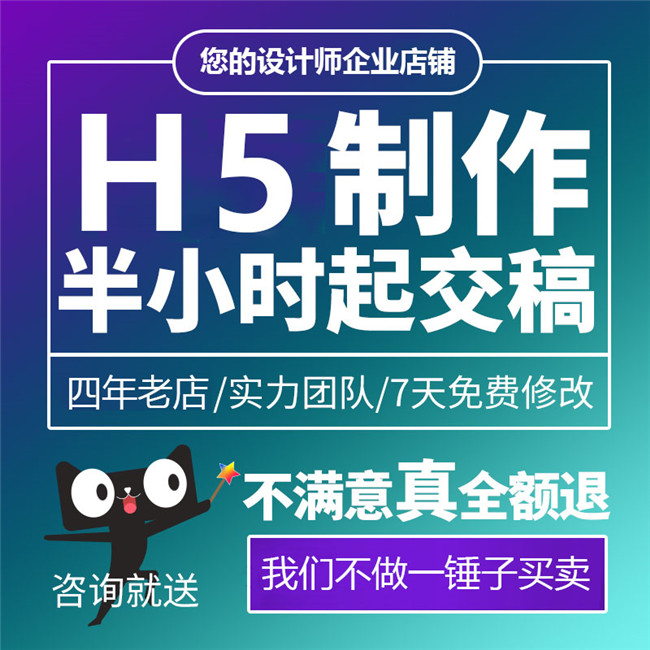
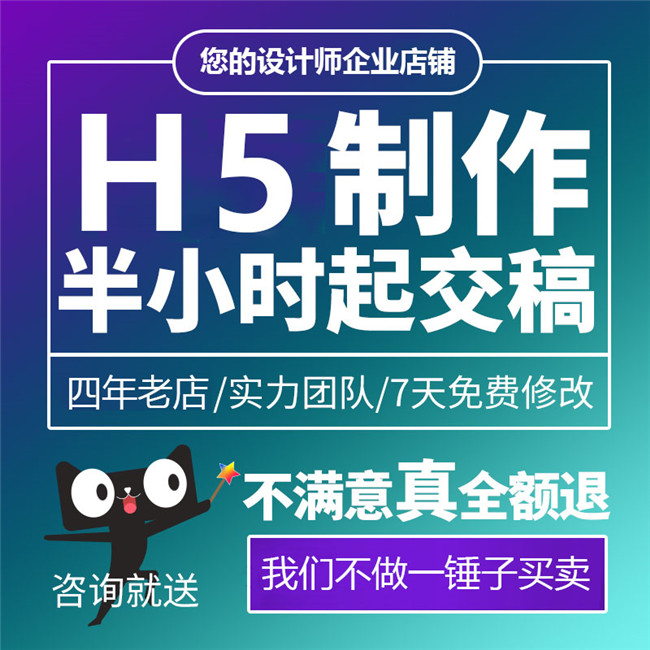
今天主要跟大家分享一些关于颜料分散装置高速分散机的结构及工作原理,和循环分散定位方式工作原理的一些题,希望对大家都有帮助到家。
为了实现经济高效的分散方法,涂料生产过程一般采用四个步骤。
预分散将部分颜料和涂料在配有搅拌器的设备中混合,产生半成品混色浆,称为混浆。
研磨分散将混合浆料通过各种研磨设备分散,得到颜料浆。
调漆用搅拌器将剩余的油漆、其他助剂、溶剂加入调漆罐中的颜料浆中,并根据需要调整颜色,以满足油漆质量要求。
片剂包装通过各种过滤设备除去机械杂质和粗颗粒,然后包装为成品。
涂料生产由过去主要是间歇式生产,现在已实现连续化生产。适合连续生产的设备,特别是研磨分散设备,近年来发展迅速。涂料的生产工艺一般根据所使用的研磨分散设备来划分,最常用的有砂磨分散工艺、辊磨分散工艺、磨分散工艺。色涂料的生产一般根据生产的品种组成专门的生产线,避免不同品种之间的干扰。
颜料分散体的制备和使用分为三个步骤预混合,即将干燥后的颜料混入涂料中并除去结块。施加足够的剪切力,使颜料聚集体分离。稀释涂料,即混合颜料。分散体用于通过混合配方中的剩余成分来制造油漆。
分布式设备
预混主要是为了混合,起到粗分散的作用。过去,涂料的研磨分散设备主要是辊磨机,辅助预混设备是各类搅拌机。近年来,主要的破碎分散设备是砂磨机,辅助设备也被高速分散机所取代。这是目前应用最广泛的预分散设备。
由于提升后旋转,高速分散机上可安装24个固定容器交替使用。高速分散机机身设有液压升降及旋转装置。液压升降装置采用齿轮油泵提供压力使机头升高。下降时,下降速度由行程节流阀控制。旋转装置可使机头360旋转。
高速分散机的关键部件是齿盘叶轮。由于叶轮的高速旋转,搅拌槽内的漆浆会引起滚动循环,产生较大的旋涡。漆浆顶部的颜料颗粒迅速螺旋下降到漩涡底部。距叶轮边缘约25至5厘米处形成紊流区域。在这个区域,颜料颗粒受到强烈的剪切力和冲击力,导致它们快速分散到漆浆中。在该区域之外,形成上下射流,使漆浆充分循环和旋转。如图5-6所示。
在高速分散机运转的初期,颜料仍然堆积在涂料中,此时采用低速进行混合,然后提高叶轮的圆周速度。
当达到约20m/s以上时应能获得满意的分散效果。但转速不宜太高。否则,漆浆会飞溅,盘式叶轮会过度暴露并与空气混合,增加动力消耗。一般情况下,叶轮的最大圆周速度约为2530m/s。分散步骤大约需要15分钟。降低速度并添加剩余成分以稀释油漆。生产乳胶漆时,乳胶不能进入分散阶段。由于大多数乳胶在高剪切力下会凝胶化,因此必须以低速率添加它们以稀释涂料相。
为了使叶轮下部区域达到层流状态,叶轮的圆周速度不能过度提高,同时必须适当提高漆浆的粘度并降低叶轮的位置。实现主要层流的最小粘度通常大于3Pas。粘度越高,施加在附聚物上的剪切应力越大,因此分散得越快。粘度应设置为电机的最大输出。
为了最大限度地提高效率,必须尽可能增加颜料的用量。只要溶剂型涂料能够稳定分散而不结块,所用基材的树脂含量越低越好。使用丹尼尔倾点,您可以估计树脂/溶剂比率,然后确定在电机最大电流下运行的油漆与颜料比率,以便在高剪切速率下具有适当的粘度。乳胶漆颜料的水分散体中常常添加水溶性聚合物,以增加分散过程中的粘度。
使用高速分散机,离心力将材料推至罐的边缘。如果研磨物料是牛顿流体且尺寸和操作条件合适,则整个物料将被均匀混合并反复通过靠近盘边缘的最高剪切区。但如果粉碎后的物料是剪切稀化的,则剪切力小,粘度高,因此罐边缘的物料顶部粘在壁上,导致混合不完全。一些研磨材料含有会剪切稀释最终油漆的颜料。为了解决壁粘附题,可以在分离后缓慢添加提供剪切稀化效果的颜料。减少粘壁题的一个好方法是让分散罐内的慢速刮刀沿罐内壁顶部旋转,高速盘在罐中心快速旋转。
高速分散机投资成本最低,不需要单独预混,稀释可在同一个罐内完成,使用更方便。有盖罐的溶剂损失较少。主要缺点是施加在颜料聚集体上的剪切应力较低,因此只能用于容易分离的颜料。
异味净化的原理简单来说就是冰箱内部的铂金异味净化装置可以散发出大量的铂金颗粒,铂金颗粒通过内循环系统分散到冰箱的各个角落,达到吸附的效果。闻。
全动力电池产业正在迈向“TWh时代”。
近日,马斯克在特斯拉电池日上提出,到2030年动力电池生产规模将达到TWh规模,单线产能将达到20GWh。这些变化将不可避免地彻底改变现有的流程和制造。
马斯克的判断绝不是空中楼阁。根据全汽车电动化、能源友好化趋势,未来几年动力电池需求将呈现显着增长。
我们看到,包括大众、戴姆勒、宝马、通用、丰田在内的几乎所有汽车企业都发出了关于电动化的明确信号,并设定了明确的目标。雄心勃勃的目标自然会增加动力电池的需求。
统计显示,为满足终端市场需求,到2022年,全动力电池规划产能将增至621GWh,未来三年将增长5倍以上。
随着产能需求快速增加,单条产线的产能计划也大幅增加。这意味着继续使用旧的工艺和设备已经不能满足您的需求。
着眼当下,动力电池制造在过去几年发生了重大变化,规模化制造正在进行中。纵观比亚迪和宁德时代的生产线,现有的工艺和设备已经不能满足要求,开始引进新的工艺和设备。
在前端均质化体系方面,高工锂电注意到,2018年以来,国内各大动力电池企业开始采用新的均质化体系工艺。
高工锂电发现均质系统颠覆了传统制浆工艺,大幅增产降耗,正在被一些大型电池企业大规模应用,并以其优异的性能被命名为“循环高效制浆系统”结构原理就完成了。
作为循环高效制浆系统的开创者和领导者,深圳市上水智能装备有限公司凭借其循环均化设备及系统的创新技术,极大地提高了均化生产效率和浆料稳定性。这让我们从幕后走向了行业的主流视角。
其中,现有电池企业迫切要求加大规模化生产,更多原因是应用新技术的制浆系统可以大幅提高电池企业效率,同时解决传统均质化浆料不稳定、能耗等题因为它可以帮助你。消耗高、污染大、占地面积大等关键题。
循环高效制浆系统的工作过程为在循环罐中添加溶剂和液体导电剂,通过给料泵将活性物质粉末、导电剂输送至高速制浆机。并且粘合剂穿过粉末。搅拌机混合均匀后,逐渐放入高速打浆机中,将粉体和液体混合,在高速打浆机中初步分散,然后通过浆料进一步分散。多次循环即可获得合格的浆料。
尚水智能高效制浆系统之所以能够大幅度提高制浆效率,主要有以下两点
1、采用“边加粉边混合”的半连续制浆工艺,让粉体在分散的同时与流动的液体接触,大大增加了粉体与液体的接触面积,防止结团,大大提高了制浆过程。制浆过程提高了粉末的润湿效率。
2、所有纸浆依次循环通过高速打浆装置,避免了因随机影响打浆效果而产生的均匀性和批次稳定性题,大幅提高打浆效率。
该均质化系统的具体主要优点是
1、显着提高生产效率。传统的混合设备需要四到六个小时才能制浆一批材料。采用循环高效制浆系统,一批物料的制浆时间可从05小时缩短为15小时。
2、提高浆料的批次稳定性。传统的双行星搅拌设备在高粘度区采用捏合,在低粘度区采用高速分散。分散量大,分散效果受概率影响,均匀性和批次稳定性较差。
尚水智能循环高效制浆设备的分散方式是粉体在中低粘度区域高效润湿、高速分散。分散量小,分散效果好,浆料稠度好。更好的。
3.节省空间。传统均质系统设备庞大,单机容量有限,导致系统占用空间较大。例如,对于容量为1200L/h的系统,传统的均质系统将需要至少三个1200L混合器。占地面积一般大于23mx7-5m,高度大于9m,而同容量的循环高效制浆系统占地约8mx6m,高度小于7m。
事实上,对提高生产效率的需求导致了涂装设备烘箱更长,这使得减少前端均质系统的占地面积成为电池公司的重要要求。
4、节省能源消耗。产能1200升/小时的循环高效制浆系统,装机功率仅159千瓦,每批制浆时间小于1至5小时,单位能耗低于30%传统的混合系统。大幅降低了电池企业的电耗。
高工锂电了解到,上水智能是国内首家引进薄膜式高速分散设备,基于先进混合分散技术消化吸收,应用于锂离子电池制浆系统的智能装备公司。尚水智能研发出的这套具有自主知识产权的循环高效制浆系统,大大提高了生产效率和浆料稳定性,降低了能耗和占地面积,并得到了国内几大电池公司的认可。
尚水智能所坚持的是深入分析客户的需求并提出的解决方案来实现其目标。我们将追随行业领先客户的脚步,不断改进和提高产品性能和服务水平,为纳米材料制造工艺提供高效、低能耗、数字化、零排放的综合解决方案。
值得一提的是,尚水智能还可以为锂电池材料制造提供双驱涂布机、高温涂布机、气流磨、高效空气混合机等创新工艺设备。
其中,上水智能双驱动粉末包衣机为国内首创,高速叶片和低速锚叶片同轴配置,通过涡流混合,可高效、均匀地包覆活性物质颗粒表面。正负极材料的涂层极大地提高了正负极材料的性能。
长期来看,未来动力电池市场潜力无限,快速捕捉技术和市场机遇成为智能装备企业现阶段的一大任务。
返混是指装置内沿某一方向流动的流体受到一定程度的影响,然后部分流体沿相反方向流动,并在流路横截面完全混合的现象。
这种混合影响装置内的流体浓度分布和停留时间分布,也影响装置的性能。因此,返混题在许多均相和多相分离和反应过程中非常重要。通常应研究示踪剂,并用涡流色散系统或佩里克数来表示返混程度。返混又称返混,是一种混合现象。狭义上理解,是指物料在连续过程中向主流相反方向移动而发生的混合。这种混合的存在影响了沿主流方向的浓度分布和温度分布,使浓度趋向于出口浓度。对于传质过程,这些浓度变化会降低浓度驱动力,从而降低传质速率。反应过程中,这种浓度变化使反应物浓度降低,产物浓度升高,从而降低了主反应速率,增加了副反应速率,降低了反应选择性。有两种描述返混的极端模型完全混合流模型和活塞流模型。如果实际返混情况与活塞流没有显着偏离,则通常使用扩散模型。如果实际返混情况偏离完全混流,则采用多级完全混流模型。在化学放大过程中,必须充分考虑根据返混程度可能发生的变化。然而,返混并不总是一个有害因素。例如,如果产物具有催化作用,并且平行副反应的级数高于主反应,则返混有些有利。返混使材料在设备中的停留时间变得均匀,从而形成停留时间分布。流量不均匀也会造成停留时间分布。因此,一些研究人员认为,广义上的返混是指在不同时间进入系统的材料的混合,包括相反的材料流,例如由于湍流和分子扩散而产生的循环流和轴向流。速度分布不均匀、停滞或“死区”、沟流引起的短路等都是导致物料在系统中停留时间不同的因素。反应器中流体返混的原因有两个。1、在连续反应器中,由于反应器内循环物料的反向运动,发生反应器内循环流与反应器内连续流的反向混合。连续釜式反应器的轴向反扩散和搅拌——2、如果反应器内物质的流速分布不均匀,反应器内的浓度分布也可能发生变化,引起回流。
发表评论